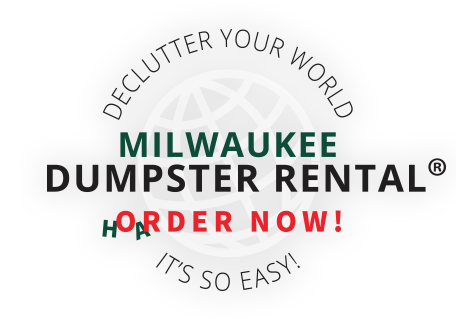
High oil prices improve asphalt shingle recycling market
by Irwin Rapoport
More and more companies are seeing the potential of using the material and products created by the recycling of asphalt roof shingles, says William Turley, the executive director of the Construction Materials Recycling Association (CMRA).
The key is that the bitumen used to hold together the asphalt shingle is made from oil, and bitumen has risen recently to $350 to $400 a ton, while only a year ago it was $200 a ton.
"Recycling has taken off because the shingles are made from bitumen, the black stuff that you use to make asphalt roads," says Turley. "We all know what the price of oil is doing now and recycling this material is very economical."
Turley participated in the 3rd Asphalt Shingle Recycling Forum, held last November in Chicago. The seminar examined the re-use of these shingles in hot mix asphalt and use in other potential markets.
The event was co-sponsored by the CMRA, Federal Highway Administration, United States Environmental Protection Agency, Asphalt Roofing Manufacturing Association, Asphalt Paving Alliance and the National Roofing Contractors Association.
"These organizations are all very supportive of recycling the shingles," says Turley.
"There was a tremendous amount of interest and information exchanged," he adds. "As well, a lot of technical data is now available on how to use those recycled shingles and their uses."
The site, www.shinglerecycling.com, was recently updated and contains the latest information on shingle recycling, including a Best Practices Guide and The Environmental Issues Associated With Shingle Recycling.
Peru, Indiana-based Recycling and Processing Equipment Inc. (RPE), a company that sells recycling equipment and performs contract work, has been recycling shingles since 1996.
The company, which sends crews and equipment to locations across the nation, is currently processing shingles in Missouri for a major company that operates asphalt plants in several states and also builds roads.
Gary Davis, RPE's operations manager has no doubt that the industry will grow.
"As time goes on, there will be a demand - probably more so for services to recycle the shingles," he says, "but there will be a certain amount of companies that will purchase equipment."
At first, shingle recycling was based on rejects from manufacturers, but now a growing segment of the materials are shingles (tear-offs) collected from roofing contractors.
"It's a very important material," says Davis. "As the price of oil goes up, shingles become black gold. When the price of oil was in the $20 a barrel range, it wasn't as big an issue as it has become today. Between tear-offs and new rejects, there are anywhere from 9 to 12 million tons a year that is going into landfills.
"It's a huge number and it would be more tear-offs than new rejects because we are just beginning to work with the tear-off market," he adds. "When we first started in 1996, we ground nearly 100 percent new rejects. With the project we are doing in Missouri, we will have ground approximately 35,000 to 40,000 tons of tear-offs by mid-February."
According to Davis, there are currently four firms nationwide that handle contract work to grind shingles that will be used for hot mix production.
Should the price of oil remain high and if enough people become involved in the industry, Davis says that a good percentage of shingles could be recycled.
"But bear in mind," he says, "that in Department of Transportation work, some of the states will allow anywhere from five to seven percent of recycled shingles. That may not include RAP (recycled asphalt pavement)."
For the Missouri contract, RPE is working with materials that were brought to a central location.
Davis says that it would not be hard for central locations to be established in states where tear-off shingles could be deposited by roofing contractors and manufacturers to await processing.
"It would require a visionary to see the need to do that," he says.
With homeowners replacing millions of roofs annually, Davis says that it would be easy for municipalities to set up locations where contractors could drop off shingles.
"If a roofer is doing a 20 to 30 square yard house," he says, "they will use a 20 yard dumpster for the shingles. A municipal yard is not impossible to establish, but it may be improbable to do at this point. Eventually everything will make a full circle and it could go that route. Right now this type of recycling is so new and in the whole scope of things, this is just catching on. If done right, this could be a closed loop system."
If not used for highways, the hot mix with shingles could be used for municipal roads, parking lots and driveways. This use depends on a given area and the economics of collecting shingles for recycling.
Shingles deposited in landfills do not break down and due to their weight, increase landfill costs for contractors.
The process to ground a shingle is simple. RPE has a bucket loader that carries them to a 550 h.p. Cat engine Bandit Beast. The pieces, when ground, range from 3/8 to 1/2 an inch. The pieces are either shipped to a facility or placed in the hot mix production process on the spot.
For tear-offs, Davis says that asphalt contractors typically receive a tipping fee, which will be a lower than if they went to a local landfill.
"That number varies across the country," he says. "Most often shingle producers drop them off at the asphalt plant they have an arrangement with. The plants are very critical because they are the ones they are taking the shingles to reduce their costs."
While some manufacturers do use shingles to produce hot mix, Davis says that there is room for growth.
But despite comments from President George Bush that the nation has to reduce its dependence on foreign oil and to conserve energy, Davis says that little is being done in terms of legislation to promote shingle recycling.
"You don't hear a lot about it," he says. "That is where the CMRA comes in."
While there is room for more shingle recycling contractors, Davis stresses that this industry involves a costly process.
"We'll wear out a machine in about 1,200 to 1,400 hours and then we have to do a major refit," he says. "It's a large expense and it takes a lot of consumable items on a day-to-day and week-to-week basis to keep one of those shingle grinders going."
Despite the cost of the hiring out a contractor, Davis says it still makes economic sense for manufacturers to use ground shingles. Manufacturers could do more to promote the use of shingles as an ingredient, he adds, but notes that some firms do not want to advertise that they use shingles to their competitors.
"That may be their edge," he says. "We are basically in the infancy of this industry."
Mike Davis, the asphalt plant manager for Barrett Paving's Michigan operations (seven asphalt production plants), notes that his facilities produce over one million tons of hot mix annually, of which about 300,000 tons is RAP and 40,000 tons is from rejected shingles.
The company uses about 30 percent of its total production for roadwork services that it provides.
"Shingles are economically viable - we do it because it lowers our costs." says Davis, "With our testing and experience on using the shingles over the years, we've actually seen a better performance of our commercial asphalt. We get less call back for cracking.
"The trend is catching on," he adds. "When I started doing this, we could collect the shingles from manufacturers, taking rejects that would go into landfills. They would pay us the equivalent of whatever the landfill fees were. Nowadays they don't even pay you. They know the value and say that each ton of shingle is roughly worth about $100 worth of asphalt."
Barrett receives shingles from GAF Corporation and Certainty Corporation, which collects shingles for processing. While it has not used tear-offs, this option is being considered as an additional source of supply.
Davis estimates that 18 million tons of tear-offs are dumped into landfills annually and that recycling those on a yearly basis would not be easy as the maximum allowance for shingles in hot mix is between six and seven percent.
When working for a previous company in Ohio from 1993 to 2003, Davis says that the state's Department of Transportation approved the use of asphalt made with shingles to be used in the road base.
"We probably took in about 40,000 tons of shingles a year, putting that in almost two million tons of hot mix asphalt," he says.
Barrett adds approximately six percent of shingles to all of its hot mix products, but the use of this additive is limited to the Michigan operations.
"I have yet to convince any of my colleagues in the other states for Barrett to do it," says Davis, who adds that a growing number of manufacturers see the benefit of using shingles.
Davis would welcome federal and state government intervention to provide incentives or mandate the use of shingles in hot mix.
"Any kind of government participation in this could overnight take this thing off," he says. "The problem is that while many of the state departments of the environment support this, on the other side, the people at the departments of transportation don't want to hear about it.
"But if somebody could wave a wand and have the two departments come together - even if they started with one percent instead of six percent, it would make a difference," he adds. "We'll work with these testing irregularities that shingles seems to cause in the asphalt. At Barrett, we already warrant the work for three to seven years. If somebody provides some encouragement or stipulation to do it on the government side, it would happen."
Davis hopes that by several states setting the example, others will follow.
He does note, however, that shingles compete with RAP, a material that has a very high recycling rate. Barrett produces hot mix products with 40 to 50 percent recycled content.
Return to Dumpster Rental News