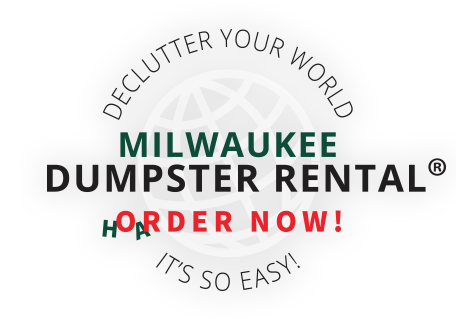
Money in dumpster recycling
With Alliant Energy of Madison, WI
Money in the dumpster: construction site recycling was part of the blueprint at the Alliant Energy headquarters project - Cover Story
C&D Recycler, May 2002 by Tom Kennedy
Alliant Energy is a power-generating company based in Wisconsin. When the company wanted to build a new headquarters in Madison, the final design was a $57 million, 341,000-square foot project on which Opus North, Milwaukee, was the winning bidder.
But, as the bidders learned, Alliant wanted more than just a new building. The company wanted to demonstrate environmental stewardship and required the winning contractor to set up and execute a program to recycle the waste generated during the construction phase.
A TEAM EFFORT
Opus North's role in recycling was to set up a program that reduced the amount of waste generated on site, reused as much material as was feasible and recycled as much of the remaining material as was possible. This policy fits in well with our own environmental commitment, and having a customer who required it fortified the position.
But we also felt that becoming proficient at recycling construction waste would provide us with a market edge over our competitors, an edge our construction company could continue to exploit in the future.
The recycling program really was a team effort. To make these kind of programs work requires top management commitment. Project manager, James Shebesta, represented Opus North. Alliant Energy was represented by a vice president who was involved in the planning process for the recycling sector.
Also involved in the planning process was a solid and hazardous waste specialist from the University of Wisconsin Extension. In addition, thanks to a grant from the Wisconsin Department of Natural Resources (DNR), WasteCap Wisconsin, Madison, a non-profit agency devoted to promoting recycling in the state, provided recycling consultant services to help us find recyclers and markets for the waste generated.
Green Valley Disposal, Delavan, Wisc., the site hauler, also did some research and provided service options for the recyclables and waste.
The goal of the project was to recycle half of all the material generated from the landfill. That meant we needed to estimate the quantity of materials generated and develop a plan to accomplish this goal. We held team meetings to determine the waste generated by the different contractors by type, estimated amount and time of generation.
For the large quantity materials, we then researched recycling options. If such an option existed for a material, we then determined if it was economically feasible to recycle it. Those parameters included the market need, the material quality and the costs of sorting and hauling. Having nearby markets is very important.
We decided to use a common approach to construction site recycling, in which bins for specific materials were placed around the site. Labeling the bins, as described below, was also critical.
EDUCATION
To make the recycling happen, our recycling team had to make it easy for the crews to recycle. In addition, we had to make sure they understood and complied with our recycling needs, and we took feedback from them on how to do it better.
One move we made was to purchase signs designating what should be placed in which barrel or roll-off. Unfortunately, the magnetic signs we placed on some of the dumpsters were not removed before they left the site, so we lost a lot of them. "A frame" signs in front of dumpsters worked well for easy identification of what material was allowed in that container. But it was constant work to remind the subcontractors of the recycling practices on a daily basis. They were not used to doing it.
The subcontractors knew from the start that recycling was a goal, as we put that in all the specs they received. In addition, aside from all the signs and labels we had on the dumpsters, there were weekly foreman and project-manager meetings to report on the progress of the recycling effort, plus meetings with the contractors to discuss results and to set up incentives for them to buy into the program.
We constantly performed site assessments to identify issues about the recycling program, to discuss with the laborers what they thought about it and to photograph and document how much recycling was being done. This monitoring is key to success in any construction site recycling project.
Alliant Energy and Opus both reported extensively in their internal communications, such as employee newsletters, about the progress of the recycling program in order to generate pride in the employees for these actions. And a national public relations campaign about this project is generating interest in other building owners and helping build C&D recycling capacity.
A RANGE OF MATERIALS
Wood, which was sent to WoodCycle, a wood recycler, for processing into a mulch product.
- Wooden spools were sent back to the manufacturer for reuse.
- Paper products (used in packaging) were handled by Green Valley Disposal, which accepted corrugated cardboard and other paper that was generated.
- Scrap metals were transferred to a scrap recycler.
- Drywall/wallboard was hauled to a farm, where it was ground (along with its paper backing) and applied to land as a soil amendment. There was a question about whether Type X drywall, which has a small amount of fiberglass in it, could be used. But testing by the University of Wisconsin proved Type X drywall was benign and would not be harmful in agricultural applications.
- Recyclables such as glass, tin and aluminum containers, as well as plastics types 1 though 7, were also collected and recycled. The consumer recyclables had their own container next to every trash container at the site.
REPORTING AND FINANCIAL AID
Because of the innovation of the program and the potential for the state to benefit from increased C&D recycling, we received a Wisconsin DNR demonstration grant to assist in the development of the implementation and reporting phases of the recycling program.
But be forewarned before applying to receive a similar grant from your state, as the reporting requirements for the grant were quite onerous and practically required a full-time person to perform.
Some details we would suggest to any construction company looking to get into these programs include some well known facts and some new ones. First, it is better to keep the material well separated at the source, as it made for easier recycling. Also, as the types of waste generated change during construction (i.e., wood during the framing process), use a time-based recycling service based on where you are in the construction cycle.
Keep the site secure to stop illegal dumping in the roll-offs. Once contaminated with outside garbage, they are difficult to clean.
In addition, we had an on-site supervisor who conducted daily site assessments and was in charge of enforcing the plan. Don't be afraid to get tough; when a sub was in non-compliance, we made the company responsible clean up the mess.
Speaking of messes, there were a few challenges. One was contamination of the cardboard waste, either by rain or other liquids. Also, caulk tubes were thrown into any nearby container, and that was the waste we had the most trouble keeping out of the recycling bins. Wood with nails was a problem for us, but most wood recyclers have magnets to handle the removal of nails in the grinding process.
Another challenge was the inexperience of all the team members involved. Neither the builder, waste hauler, nor general or sub contractors had ever participated in a construction site recycling program before. We all learned a lot, and if we do it again, it will be done more efficiently. Now we know what can be recycled easily and where the operations to do it are.
That was another obstacle: the lack of facilities available to process the waste. We suspect that if more companies recycle construction site waste, then a larger recycling infrastructure will be developed.
BOTTOM LINE AND BENEFITS
Here is what it takes to make a construction site recycling program work:
- Team commitment from the building owner, hauler and all contractors;
- Assigning one person clear responsibility for recycling, similar to how it is done for safety;
- A thorough knowledge of the recycling infrastructure in the area before beginning;
- Requirements for recycling must be integrated into the project specifications;
- Requests must be made on bid forms for alternate/reduced or zero packaging of materials, such as spool returns, blanketed furniture, etc.; and
- Contractors should build a system to routinely recycle at the construction site.
What are the benefits of recycling? It satisfies an owner's commitment to the environment and provides them with some public relations value. We believe through reduced documentation requirements and careful implementation, construction site recycling can be cost-effective. It is very possible project costs can be reduced through recycling. In fact, for a contractor recycling can be a very effective marketing tool in an environmentally conscious world.
RELATED ARTICLE: Recycling Results, Alliant Energy HQ
(Completed in February 2002)
- 494 tons recycled, out of 733 total tons of excess material, for a 67.8 percent recycling rate by weight
- 4,853 cubic yards of material recycled out of 6,750 total cubic yards of excess material, for a 71.9 percent recycling rate by volume
The full case study will be available from WasteCap (www.wastecap.com) in the summer of 2002.
On-site Grinding of Construction Waste? A New Twist
Waste is an expensive part of a construction job because the contractor pays for it five times: when material is bought and when waste is created, cleaned up, hauled and landfilled. Grinding on-site removes the last two steps and reuses the material on-site.
The concept is simple, according to Ken Patterson, owner of Patterson Services, a company that grinds on-site, and Packer Industries, a grinder manufacturer. Both companies are in the Atlanta area. Waste wood, gypsum wallboard, bricks and blocks are ground and the finished product is used in various ways on-site.
Patterson says a primary step is separating the material to be recycled to prevent contamination. He suggests recycling in conjunction with the project stages to avoid contamination.
Patterson says a 2,000-square-foot home produces about 4- to 5-cubic yards of wood chips. This wood can be reused on-site as mulch for decorative purposes or for erosion control. It also can be used to control dust or to create a path to the job site, keeping dirt out of the building.
Soil amendment is the primary use for the recycled gypsum wallboard. Gypsum increases the available calcium and sulfur, improves soil tilth and root penetration, particularly in soils high in clay, and helps treat sodic soils. Patterson says the gypsum particle size should be 1-inch minus, but application rates vary depending on the soil. Soil samples determine the correct application rate, but the range is usually from 2 to 8 tons per acre.